The Aluminim alloy AlSi10Mg is very well suited for additive manufacturing Additive Manufacturing ("AM") with the SLM process (Selective SLM process (Selective Laser Melting). SLM is also known as "Laser Powder Bed Fusion" (LPBF) or "Direct Metal Laser Melting" (DMLS). In this process, free-form surfaces such as flow parts can be produced very cost-efficiently. can be produced very cost-effectively.
-
Free-form made from aluminium
-
Aviation
Aerodynamic AM lightweight components can also be used in aviation thanks to suitable thermal post-processing, lightweight aerodynamic can also be used in aviation. For the cyclic load, the surface surface quality is of central importance. Thanks to suitable finishing processes such as blasting, trowalising, electro- and plasma polishing, an optimal optimal starting position for the required application can be created.
-
Costs
In additive manufacturing, the costs are driven by the volume required for the component. Through suitable application of lightweight construction methods (e.g. honeycomb honeycomb structures or cavities), the volume - and therefore and therefore also the costs of components - can be can be significantly reduced.
-
Function integration
Additive manufacturing makes it possible to integrate functions directly into a single component. This downstream joining steps can be greatly reduced. Channels that follow a surface close to the contour, e.g. for cooling or cooling or measuring purposes, can be integrated into a housing which can also be customised with a serial number or labelling with a serial number or customer name. labelling.
-
Superalloys
Hot gas components such as burners, turbines or swirlers made of Superalloys are well suited to additive manufacturing. A component is often validated during several iterations validated over several iterations before series production can begin. We often use often use the IN718 alloy, but we are also familiar with other alloys are not unfamiliar to us. Ask us about your your requirements.
-
Space travel and process documentation
We are proud of the fact that various satellites orbiting the earth orbiting the earth with components from ProtoShape. In addition to production with the SLM process, we have also taken over the CNC post-processing as well as the quality inspection using X-rays and CT scans. Our process documentation enables traceability right back to the powder. powder.
-
3D scanning: quality control and reverse engineering
The geometry of the free-form surfaces of 3D printed components can best be checked using 3D scanning. scanning. When used for quality control and reverse engineering engineering of components in the range up to 500mm, an accuracy accuracy of around 50um can be achieved.
-
Courses for design for additive manufacturing
So that you can make your components fit for series production we offer courses. You will get an overview of the technology, find out the limits, learn the basics for design for AM and conclude with hand-on training. training.
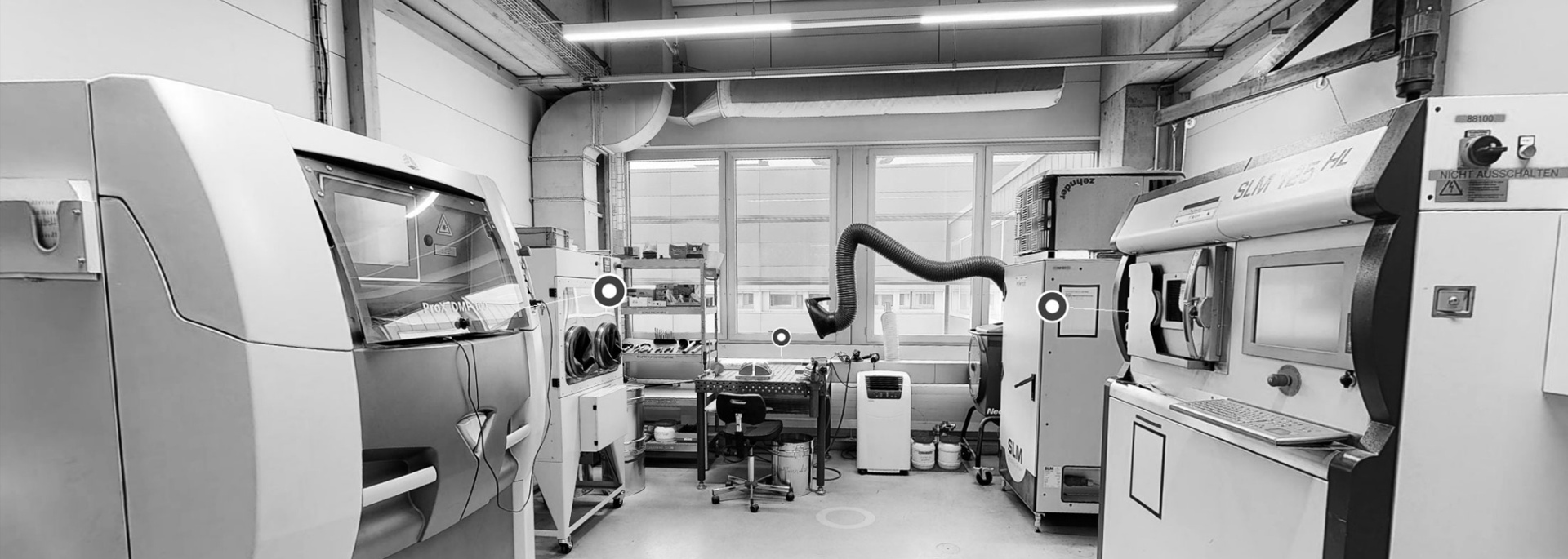
ProtoShape on the Indu 4.0 portal
3D tourThe ProtoShape 3D-Printing AG is one of the pioneers in 3D metal printing. It specializes in producing single components and functional prototypes and offers the manufacturing of series parts.
In 2012
Dr. Felix Reinert founded ProtoShape GmbH and started the operational activities, rented by Max Horlacher AG in Ennetbaden/AG
2013
Moved to Klingnau
2014
Start as a sales agent for SLM Solutions
2015
Start of production of satellite components and turbine wheels for ABB
2016
Moved to Nidau-Biel in the Switzerland Innovation Park
2017
Start of production of components for Formula 1
2018
Acquisition of a dual-laser machine
2019
Start of the high-tech output for aerodynamics applications
2020
Foundation of ProtoShape 3D-Printing AG
2020
Joining the SwissFactory.Group, Moved to Neuenegg/BE,
2021
New room with room air purification
2022
Strategic orientation towards series production, focus on "material assigned machines"
2023 Investments in production, increase in series components